Specialist Recommendations on What is Porosity in Welding and How to Resolve It
Specialist Recommendations on What is Porosity in Welding and How to Resolve It
Blog Article
Comprehending Porosity in Welding: Discovering Reasons, Results, and Prevention Techniques
Porosity in welding is a relentless obstacle that can significantly influence the high quality and honesty of welds. As professionals in the welding market are well aware, understanding the causes, impacts, and avoidance techniques associated with porosity is vital for accomplishing durable and dependable welds. By diving right into the origin triggers of porosity, analyzing its damaging effects on weld high quality, and exploring efficient prevention strategies, welders can improve their knowledge and skills to produce top quality welds constantly. The elaborate interaction of elements adding to porosity needs a comprehensive understanding and a proactive technique to make certain successful welding end results.
Typical Root Causes Of Porosity
Contamination, in the form of dust, grease, or rust on the welding surface, creates gas pockets when heated, leading to porosity in the weld. Incorrect shielding occurs when the shielding gas, typically made use of in processes like MIG and TIG welding, is incapable to completely safeguard the molten weld swimming pool from reacting with the surrounding air, resulting in gas entrapment and subsequent porosity. Furthermore, poor gas insurance coverage, commonly due to wrong flow prices or nozzle positioning, can leave parts of the weld unsafe, enabling porosity to form.
Effects on Weld Top Quality
The existence of porosity in a weld can considerably endanger the general high quality and stability of the welded joint. Porosity within a weld develops voids or dental caries that weaken the framework, making it more at risk to breaking, rust, and mechanical failure.
Furthermore, porosity can hinder the effectiveness of non-destructive testing (NDT) techniques, making it testing to detect various other problems or gaps within the weld. This can bring about considerable security problems, especially in crucial applications where the structural integrity of the bonded parts is paramount.
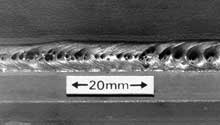
Prevention Techniques Overview
Offered the destructive impact of porosity on weld top quality, efficient avoidance techniques are crucial to maintaining the structural honesty of welded joints. In addition, choosing the appropriate welding parameters, such as voltage, present, and take a trip rate, can aid reduce the danger of porosity development. By including these avoidance methods right into welding methods, the event of porosity can be significantly lowered, leading to more powerful and a lot more trusted welded joints.
Significance of Correct Shielding
Correct securing in welding plays a crucial function in preventing atmospheric contamination and guaranteeing the stability of welded joints. Protecting gases, such as argon, helium, or a blend of both, are generally utilized to secure the weld swimming pool from responding with components in the air like oxygen and nitrogen. When these responsive aspects come right into contact with the hot weld pool, they can trigger porosity, resulting in weak welds with lowered mechanical buildings.
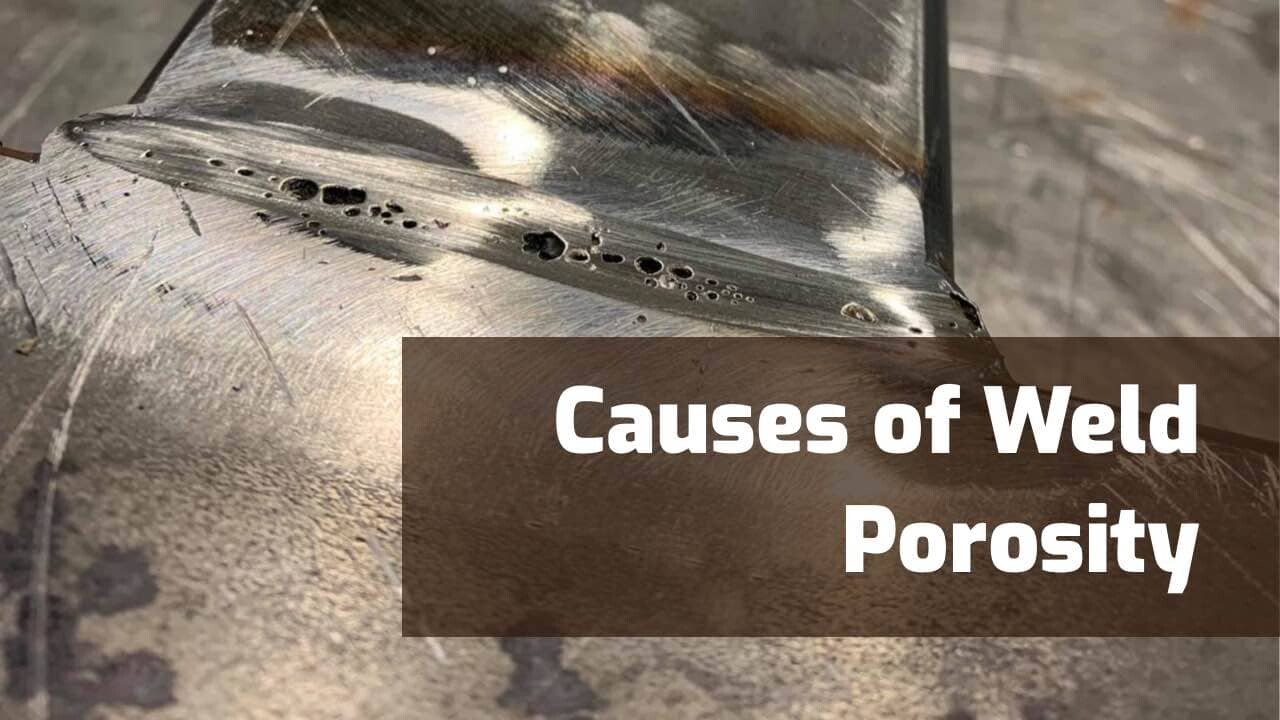
Inadequate shielding can cause numerous issues like website link porosity, spatter, and oxidation, jeopardizing the structural stability of the bonded joint. Adhering to correct shielding practices is important to produce top notch welds with minimal issues and ensure try here the long life and dependability of the welded parts.
Tracking and Control Techniques
How can welders effectively check and manage the welding process to guarantee ideal results and stop problems like porosity? By continuously keeping track of these variables, welders can determine discrepancies from the excellent problems and make immediate changes to stop porosity development.

Additionally, carrying out appropriate training programs for welders is necessary for monitoring and controlling the welding process successfully. What is Porosity. Enlightening welders on the importance of preserving consistent specifications, such as correct gas shielding and take a trip speed, can aid avoid porosity issues. Regular assessments and qualifications can additionally ensure that welders are proficient in tracking and regulating welding procedures
Furthermore, using automated welding systems can boost monitoring and control capabilities. These systems can precisely regulate welding specifications, decreasing the likelihood of human mistake and guaranteeing consistent weld top quality. By incorporating advanced surveillance innovations, training programs, and automated systems, welders can click this link successfully check and manage the welding procedure to decrease porosity problems and attain high-grade welds.
Verdict
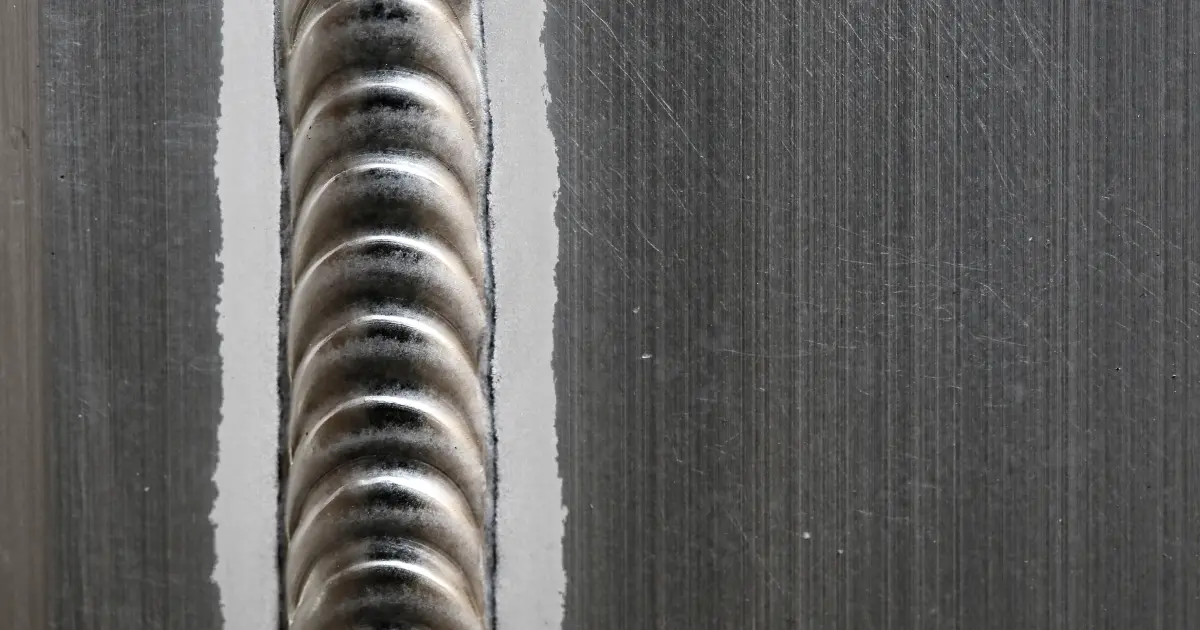
Report this page